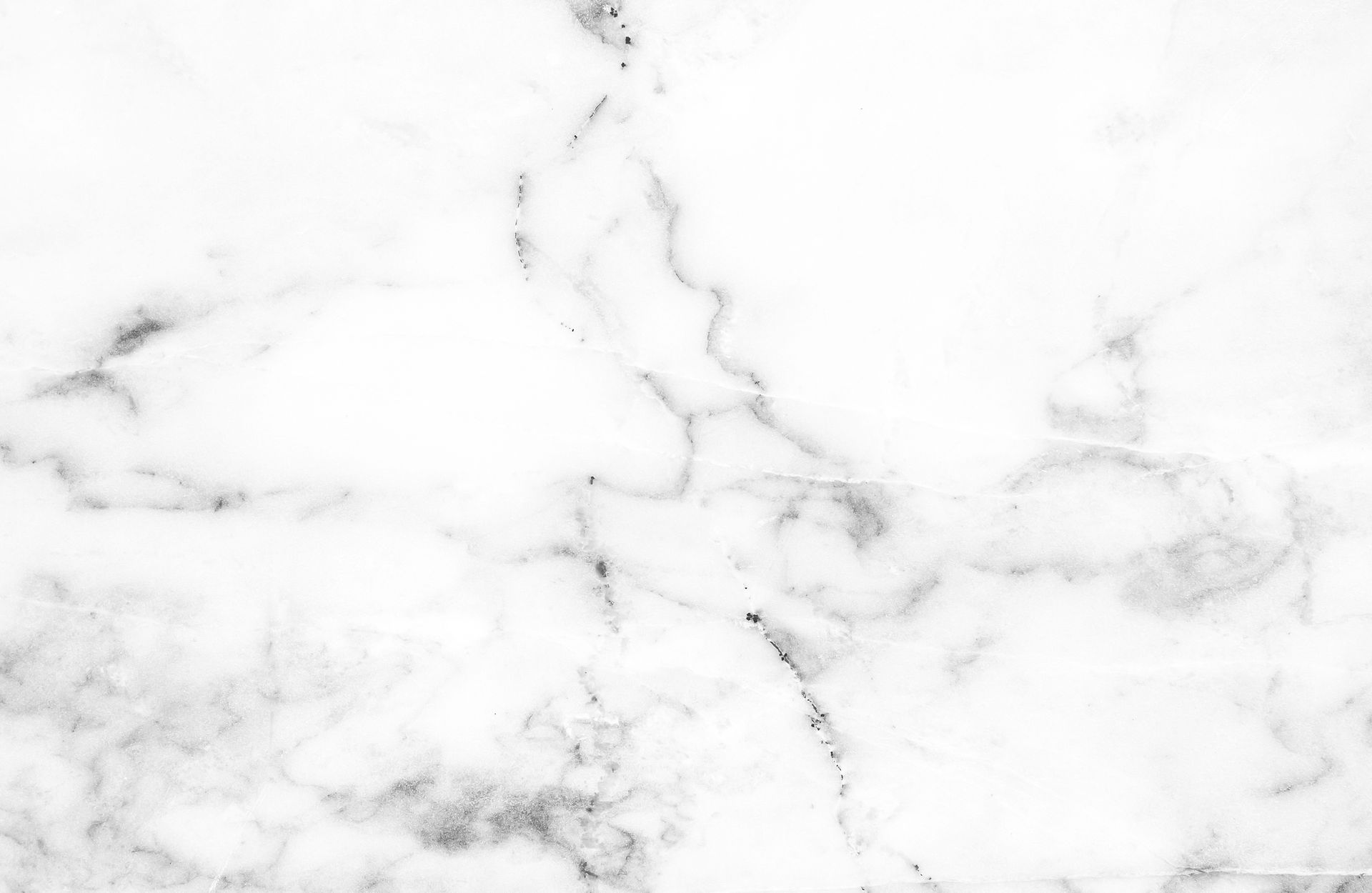

Making A Difference
Improving Lives, Manageing Risk, Maximizing Opportunities & Adding Value
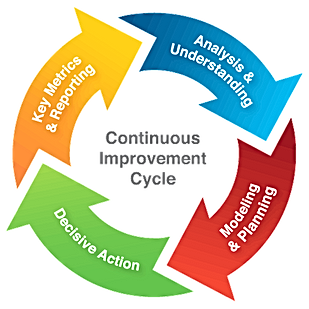
EH&S Objectives & Strategies
Leading manufacturing companies do not become industry leaders and retain that position simply by meeting financial targets. The key to leadership longevity is broader business performance, and a key component of that is a value added ESH programs - protecting people, processes, operations and the environment in which we operate.
To achieve the HS&E aspects of the Altus Pro plans and sustain an HS&E management system we will focus on the following major leadership objectives:
-
Visible demonstrated management commitment
-
Clear, meaningful policies and procedures
-
Challenging goals
-
Implement meaningful HSE tools and practices
1. Visible, demonstrated management commitment
-
Most, if not all, manufacturing companies have an individual, or an entire department, devoted to HS&E. While this may seem to encourage a focus on HSE practices, it can actually hinder safety performance. Company leaders must communicate through their words and actions that HSE is of critical importance throughout their company and not relegate it to the oversight of one person or department.
-
Integrating safety goals with other business goals can be difficult when companies strive to achieve their optimum business performance and meet lean manufacturing targets and aggressive profit goals. However, management can take actions to underscore their commitment to safety. By doing this, it is clear that it is not just the direct supervisors or line managers who are concerned with safety. It starts at the highest level of company management
​
2. Clear, meaningful policies and principles
-
Policies and procedures must reflect the reality of the business and have relevance to everyday working conditions within our company. More important than quantity is ensuring that every policy and procedure is understood and accepted by every employee. Accountability is another critical aspect of a strong safety culture. Everyone must be accountable for HSE aspects, even those at the senior leadership level. The policies must instill in every individual that believing that all injuries and illnesses are preventable; therefore, one of core HSE’s internal guiding principles is to strive for zero workplace injuries. That said, many manufacturing companies believe the nature of their industry is such that injuries are inevitable. This can become a self-fulfilling prophecy when a company is willing to accept that a certain number of injuries will always occur. The only acceptable long-term HSE goal for your HSE organization is ZERO injuries and nothing less – ever.
3. Challenging goals and objectives
-
A ZERO- Injury approach to safety requires your EHS leaders to establish safety goals that challenge employees, and to inspire the workforce to reach them. Managers must communicate regularly with line workers regarding goals and objectives and offer feedback on performance.
-
The enemy of greatness in safety is being "good-enough". When this happens, complacency may set in. Once a company has met the desired level of safety performance and company leaders believe the organization is “safe enough”, safety often becomes less of a priority. When company goals and plans stop challenging the workforce to operate with the highest safety standards possible, inevitable the level of safety performance stalls, if not deteriorates. Employees will achieve the level of performance that leaders demonstrate they are willing to accept.
​
4. Implement meaningful HSE Tools and Practices
-
Setting high performance standards is essential for your organization in order to ensure growth. Most companies set high performance standards as they relate to business goals, such as the number of units produced on a daily or monthly basis, or the amount of revenue expected for the quarter. These expectations these same type of expectations are communicated widely throughout your HSE organization.
-
Safety performance standards are no different. Your HSE management system must institute high safety performance standards and make sure they are communicated clearly and regularly to all employees.
-
To ensure that the safety performance standards are high, consider the difference between being “legal” and being safe. If a manufacturing company is being legal, it is complying with all regulatory standards. In fact, this is the common standard, and most companies are at this level of compliance. However, complying with all regulatory standards does not guarantee an injury-free workplace.
-
Being merely safe requires your organization to go beyond compliance and to take any and all necessary measures to ensure zero workplace injuries. While being safe constitutes high standards of safety performance, being legal could be considered the base level of acceptable compliance…this mind set is must not acceptable within the your HSE organization.
-
The following are standard tools and practices, should be implemented to facilitate the reduction of the current injury rates:
-
Timely reporting of HSE incident data
-
Assure that all required regulatory reporting is accomplished (e.g. Air, Haz-Mat, SWPP, Industrial Discharge, OHSA, etc.)
-
Implementation of the Balanced Score Card
-
Training – emphasis on new hires
-
Monthly workplace inspection
-
Toolbox meetings – Daily (goal), minim weekly
-
Implementation of the “High-5” process
-
Caught
-
Contact
-
Strike
-
Fall
-
Overexert
-
-
Job Hazard Analyses (JHA) – For all processes and work activities
-
House keeping
​
Conclusion
The achievement of extraordinary outcomes through these initiatives is not a destination; but will be an ongoing and richly rewarding journey. The HSE aspect of these initiatives are key element to your success. By insisting on high HSE performance standards, your leaders and all employees demonstrate that working safely is just as important as meeting productions, cost and quality standards. If the employees of the your organization settle for lower standards (less than ZERO Injuries), we must be prepared for the results: workplace injuries, illnesses or even fatalities.